球墨铸件的注意事项
1.加入孕育剂进行孕育处理
2.球墨铸件流动性较差,收缩较大,因此需要较高的浇注温度及较大的浇注系统尺寸,合理应用冒口,冷铁,采用顺序凝固原则
3.进行热处理
4.严格要求化学成分,对原铁液要求的碳硅含量比灰铸铁高,降低球墨铸件中锰,磷,硫的含量
5.铁液出炉温度比灰铸铁高,以补偿球化,孕育处理时铁液温度的损失
6.进行球化处理,即往铁液中添加球化剂
球墨铸件的防腐直接关系到管道的长期的使用性和性,因此是衡量管网技术及运行状况的一个重要指标。因铸铁中存在石墨,球墨铸件中的石墨以球状形式存在,并不影响基体材料的力学和机械性能,但据10个典型城市结果显示,我国城镇供水管网静漏失率达到12~13%,远远超过了要求城市漏失率控制在6%以下的标准,所以管道防腐一直是我们当前一个热门的课题。
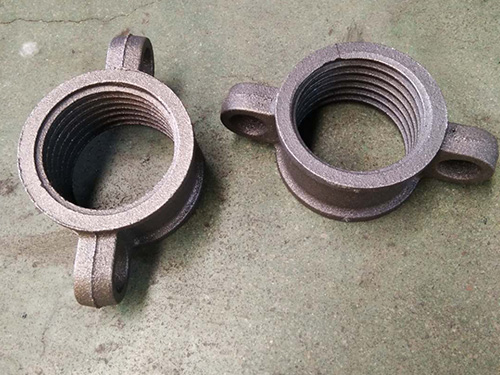
球墨铸件研究现状和常见缺陷的防止
【一】、球墨铸铁研究现状
我国关于球墨铸铁领域的研究与应用发展的比较快,从1950年研制成功至今,我国球墨铸铁年产量不断突破新高,2009年已经达到870万吨,居世界第一位。我国球墨铸铁领域的科研工作者经过几十年的努力在球墨铸铁的生产过程中取得多项技术突破和创新。
国内外科技研发人员从石墨的形核机理分析球化处理和孕育处理工艺对石墨形核和长大的影响,超声波技术,热分析技术和计算机技术的应用,合金化技术,磁场处理技术以及半固态处理技术的研发均取得了丰厚的成果。 随着研究者对球墨铸铁的研究越来越深入,球墨铸铁已经在许多领域得到广泛应用。球墨铸铁相关领域的快速发展能体现在工业生产和制造方面与日常生活及应用方面都得益于研究人员对球墨铸铁基础方面的研究所付出的努力。
20世纪70年代初期,中国、美国、芬兰几乎同时宣布已经成功研制了奥氏体-贝氏体球墨铸铁(ADI)。奥氏体-贝氏体球墨铸铁具有高强度、高韧性、高耐磨性的特点,其抗拉强度高达1000MPa。奥氏体-贝氏体球墨铸铁具有很高的经济效益和社会效益,正在逐步取代合金钢,用于制造力学性能要求较高的齿轮和各种结构件。
GF公司近年发布消息,声称已经成功研制了以硅和硼作为合金化元素并且在铸态下具有高强度和高韧性的球墨铸铁,即SiboDur球墨铸铁。SiboDur球铁在具有高强度的同时保证了高韧性,其综合力学性能远高于传统珠光体-铁素体球铁,在制造承受冲击载荷较大的铸件过程中具有广阔的应用前景。
我国研究人员成功研制了铝与硅合金化的耐热球墨铸铁RQTAL5Si5,适用于各种高温工作环境。RQTAL5Si5耐热球墨铸铁高温作业寿命比灰铸铁高2倍,比普通耐热铸铁高1倍,并与日本研发的Cr25Ni13Si2耐热钢的使用寿命相当。
【二】、球墨铸铁件常见缺陷的防止
1、夹渣
球墨铸铁的渣有一次渣和二次渣两种,一次渣一般比较容易防止,措施是严格扒渣,浇注时挡渣,浇注系统考虑挡渣措施,使用滤网等。二次渣是铁液在型腔内流动过程产生的,防止这种渣要比防止一次渣难度大,通过多年的不断探索,我厂已较彻底地解决了二次渣的问题,主要措施可以概括为下列几条:(1)采用铸造焦化铁提高铁液的温度;(2)降低原铁液的含硫量;(3)大型曲轴原铁液脱硫;(4)提高浇注速度。
2、皮下气孔
降低型砂水分和提高浇注温度是防止皮下气孔的基本条件。同时球化剂和孕育剂使用前烘干,在铸件尾端设溢流冒口排放冷铁液等措施对防止皮下气孔有一定的效果,但不明显,根据我厂经验,提高单件浇注速度是防止轴类铸件皮下气孔的有效措施,至于各种曲轴的单件浇注速度,与铸件大小、长短、浇注温度高低和型砂水分都有关系。在一定的浇注温度和型砂水分条件下,铸件越是细长,单件浇注速度越应提高,反之可以适当降低。
3、缩松和缩孔
在不致引起石墨漂浮的前提下,尽量提高碳当量。球铁曲轴选用的碳当量为4.4%~4.55%。
尽量提高铸型刚度。型腔表面的紧实度固然重要,而砂型背面的紧实度亦不可忽视。
球铁曲轴采用湿砂型铸造一定要用冒口补缩,无冒口工艺对湿砂型是不合适的。
适当使用冷铁,强化热节部位的冷却,使热节中心向球墨铸件内部迁移。
4、石墨漂浮
众所周知,碳当量过高会引起石墨漂浮,但到底碳当量高到多少时才会产生石墨漂浮,根据我厂经验及有关资料,当碳当量超过4.55%时,石墨漂浮开始出现,随着碳当量的继续增长,漂浮层成正比增加。当碳当量相同时,球墨铸铁件越厚,漂浮层也越厚。为防止石墨漂浮,主要措施为,严格配料,加强熔炼控制。
5、球化不良
主要措施有下列三项:
(1)控制原铁液硫量,减少其波动范围。通过加强严格的炉料管理,严格冲天炉配料和操作,原铁液硫量一般稳定在0.04%~0.06%之间。
(2)根据铁液温度调整球化剂成分,使合金的反应性能适中,同时严格操作,使球化处理反应时间保持在1.5~2.5min,确保球化剂吸收率稳定在一定范围内。
(3)适当控制残余稀土量。要保证球化良好,除了要有足够的残余镁量外,还要求Mg残/RE残≥1,而且,随着铸件壁厚增大,此比值亦应相应增大。目前我厂的控制范围为0.015%~0.04%RE残,0.04%~0.06%Mg残。
泊头市艺兴铸造厂(http://www.btyxzz.com)主要产品有搅拌机配件、灰铁铸件、减速机齿轮、机械加工、数控车床加工等业务。
1.加入孕育剂进行孕育处理
2.球墨铸件流动性较差,收缩较大,因此需要较高的浇注温度及较大的浇注系统尺寸,合理应用冒口,冷铁,采用顺序凝固原则
3.进行热处理
4.严格要求化学成分,对原铁液要求的碳硅含量比灰铸铁高,降低球墨铸件中锰,磷,硫的含量
5.铁液出炉温度比灰铸铁高,以补偿球化,孕育处理时铁液温度的损失
6.进行球化处理,即往铁液中添加球化剂
球墨铸件的防腐直接关系到管道的长期的使用性和性,因此是衡量管网技术及运行状况的一个重要指标。因铸铁中存在石墨,球墨铸件中的石墨以球状形式存在,并不影响基体材料的力学和机械性能,但据10个典型城市结果显示,我国城镇供水管网静漏失率达到12~13%,远远超过了要求城市漏失率控制在6%以下的标准,所以管道防腐一直是我们当前一个热门的课题。
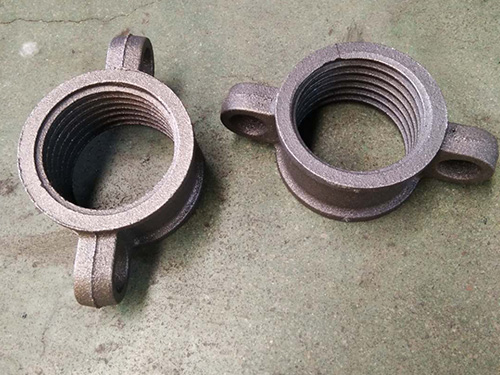
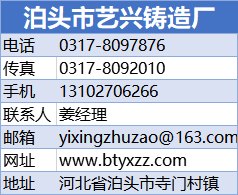
【一】、球墨铸铁研究现状
我国关于球墨铸铁领域的研究与应用发展的比较快,从1950年研制成功至今,我国球墨铸铁年产量不断突破新高,2009年已经达到870万吨,居世界第一位。我国球墨铸铁领域的科研工作者经过几十年的努力在球墨铸铁的生产过程中取得多项技术突破和创新。
国内外科技研发人员从石墨的形核机理分析球化处理和孕育处理工艺对石墨形核和长大的影响,超声波技术,热分析技术和计算机技术的应用,合金化技术,磁场处理技术以及半固态处理技术的研发均取得了丰厚的成果。 随着研究者对球墨铸铁的研究越来越深入,球墨铸铁已经在许多领域得到广泛应用。球墨铸铁相关领域的快速发展能体现在工业生产和制造方面与日常生活及应用方面都得益于研究人员对球墨铸铁基础方面的研究所付出的努力。
20世纪70年代初期,中国、美国、芬兰几乎同时宣布已经成功研制了奥氏体-贝氏体球墨铸铁(ADI)。奥氏体-贝氏体球墨铸铁具有高强度、高韧性、高耐磨性的特点,其抗拉强度高达1000MPa。奥氏体-贝氏体球墨铸铁具有很高的经济效益和社会效益,正在逐步取代合金钢,用于制造力学性能要求较高的齿轮和各种结构件。
GF公司近年发布消息,声称已经成功研制了以硅和硼作为合金化元素并且在铸态下具有高强度和高韧性的球墨铸铁,即SiboDur球墨铸铁。SiboDur球铁在具有高强度的同时保证了高韧性,其综合力学性能远高于传统珠光体-铁素体球铁,在制造承受冲击载荷较大的铸件过程中具有广阔的应用前景。
我国研究人员成功研制了铝与硅合金化的耐热球墨铸铁RQTAL5Si5,适用于各种高温工作环境。RQTAL5Si5耐热球墨铸铁高温作业寿命比灰铸铁高2倍,比普通耐热铸铁高1倍,并与日本研发的Cr25Ni13Si2耐热钢的使用寿命相当。
【二】、球墨铸铁件常见缺陷的防止
1、夹渣
球墨铸铁的渣有一次渣和二次渣两种,一次渣一般比较容易防止,措施是严格扒渣,浇注时挡渣,浇注系统考虑挡渣措施,使用滤网等。二次渣是铁液在型腔内流动过程产生的,防止这种渣要比防止一次渣难度大,通过多年的不断探索,我厂已较彻底地解决了二次渣的问题,主要措施可以概括为下列几条:(1)采用铸造焦化铁提高铁液的温度;(2)降低原铁液的含硫量;(3)大型曲轴原铁液脱硫;(4)提高浇注速度。
2、皮下气孔
降低型砂水分和提高浇注温度是防止皮下气孔的基本条件。同时球化剂和孕育剂使用前烘干,在铸件尾端设溢流冒口排放冷铁液等措施对防止皮下气孔有一定的效果,但不明显,根据我厂经验,提高单件浇注速度是防止轴类铸件皮下气孔的有效措施,至于各种曲轴的单件浇注速度,与铸件大小、长短、浇注温度高低和型砂水分都有关系。在一定的浇注温度和型砂水分条件下,铸件越是细长,单件浇注速度越应提高,反之可以适当降低。
3、缩松和缩孔
在不致引起石墨漂浮的前提下,尽量提高碳当量。球铁曲轴选用的碳当量为4.4%~4.55%。
尽量提高铸型刚度。型腔表面的紧实度固然重要,而砂型背面的紧实度亦不可忽视。
球铁曲轴采用湿砂型铸造一定要用冒口补缩,无冒口工艺对湿砂型是不合适的。
适当使用冷铁,强化热节部位的冷却,使热节中心向球墨铸件内部迁移。
4、石墨漂浮
众所周知,碳当量过高会引起石墨漂浮,但到底碳当量高到多少时才会产生石墨漂浮,根据我厂经验及有关资料,当碳当量超过4.55%时,石墨漂浮开始出现,随着碳当量的继续增长,漂浮层成正比增加。当碳当量相同时,球墨铸铁件越厚,漂浮层也越厚。为防止石墨漂浮,主要措施为,严格配料,加强熔炼控制。
5、球化不良
主要措施有下列三项:
(1)控制原铁液硫量,减少其波动范围。通过加强严格的炉料管理,严格冲天炉配料和操作,原铁液硫量一般稳定在0.04%~0.06%之间。
(2)根据铁液温度调整球化剂成分,使合金的反应性能适中,同时严格操作,使球化处理反应时间保持在1.5~2.5min,确保球化剂吸收率稳定在一定范围内。
(3)适当控制残余稀土量。要保证球化良好,除了要有足够的残余镁量外,还要求Mg残/RE残≥1,而且,随着铸件壁厚增大,此比值亦应相应增大。目前我厂的控制范围为0.015%~0.04%RE残,0.04%~0.06%Mg残。
泊头市艺兴铸造厂(http://www.btyxzz.com)主要产品有搅拌机配件、灰铁铸件、减速机齿轮、机械加工、数控车床加工等业务。